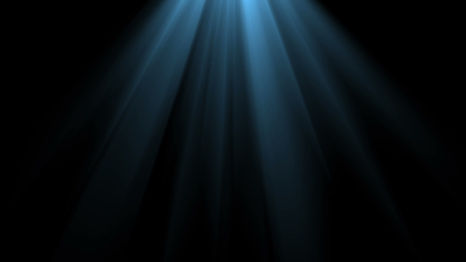


.jpg)



The Original House of Parkerizing
since 1918
NOW OFFERING BLACK OXIDE COATINGS!!
for carbon steel
A Brief History of Parker Rust-Proof

In October of 1918, The Parker Rust-Proof Company of Ohio opened as a job shop licensee of the Parker Rust-Proof Company of Detroit MI. During the next several years, there were tremendous breakthroughs and discoveries in the conversion-coating, rust-proofing process, and it was eagerly adopted by the automotive and appliance industries. In addition to combating corrosion on firearms, clients used it to promote adhesion under paint and rubber bonding, for permanent lubrication on gears and bearings, and during metal forming and forging operations.
​During World War II, Parker also played an important role in the defense industry, as our coatings were applied to components of armaments, ammunition, airplanes, boats, tanks, stampings and fasteners. We celebrated our first century of service in 2018, and are the only remaining original job shop licensee, still applying the genuine Parkerizing, Parco Lubrite, and Bonderite/Bonderlube coatings developed by our namesake.

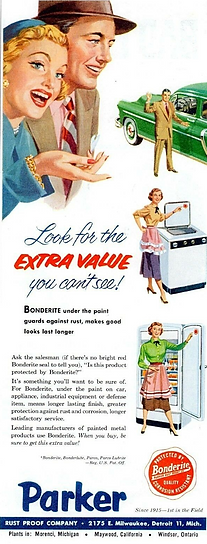

Where We Are Today


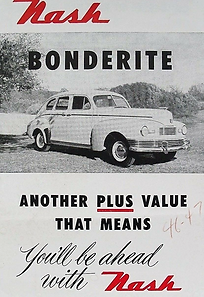
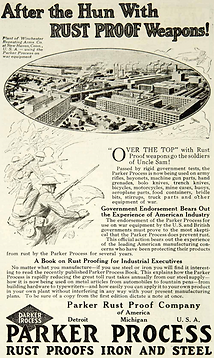
With more than 400 years of collective experience, our current team has acquired experience and technical knowledge unequaled in our field. Acquiring updated equipment and building our own tooling in-house allows us to offer fast on-boarding of new jobs and a competitive quality advantage.
Our metal finishing specialties include:
​
-
zinc and manganese phosphate coatings
-
reactive and non-reactive lubricant soaps
-
passivating
-
dry film lubricants
-
blackening
-
spray coating
-
blasting
-
deburring
-
cleaning
​
See our capability sheet HERE
Both barrel and rack processing of production quantities and small lots of ferrous and non-ferrous material is available; our four automated and manual processing lines can accommodate parts as large as 20 feet in length and as heavy as four thousand pounds. Last year, we processed more than 16,000,000 pounds of product, which makes us one of the largest phosphate coaters in the U.S.!
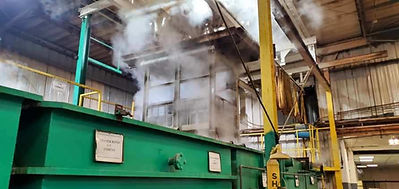

Acquiring updated equipment and building our own tooling in-house allows to offer fast on-boarding of new jobs and a competitive quality advantage. Regardless of the part or lot size, each order receives careful review and handling, quality treatment and prompt service. We are highly committed to meeting the aerospace, nuclear, military and industrial specifications required by our customers and have undertaken a rigorous schedule of quality testing and process development to accomplish this.


Our trained and experienced laboratory staff stands behind their certifications. Each load is scrutinized for visual defects and subjected to the most rigorous tests in the industry before you receive it, so you never have to worry that your customer will be disappointed. Our customers trust us to do final inspection and, in many cases, package barcode, and ship the product to the final user without ever seeing the finished material. This improves your bottom line by minimizing inspection, transportation, and inventory costs. We coat to over 500 industrial, military, aerospace, and nuclear specifications, but if you don’t see the one you are looking for on our website, we can develop and write a unique specification just like we have done for Cummins Engine and many other customers.

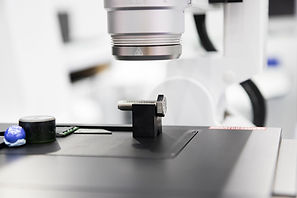
Today, Parker’s continuing expansion into our new 75,000 ft² annex, along with our dedication to the highest quality standards in the industry and a strong emphasis on process control, problem prevention, and customer service has made us the first choice in metal finishing for customers around the world.


